[ Metamaterial Strain Gauge ]

SG / 2001
Multi-Directional Sensing in Soft Robot
A common problem in soft robotics is the inability to robustly sense the movement and position of the flexible materials that make up the body of the robot. Sensors made of compatible materials like conductive silicone often suffer from hysteresis and are unable to differentiate between the various forces applied to them.



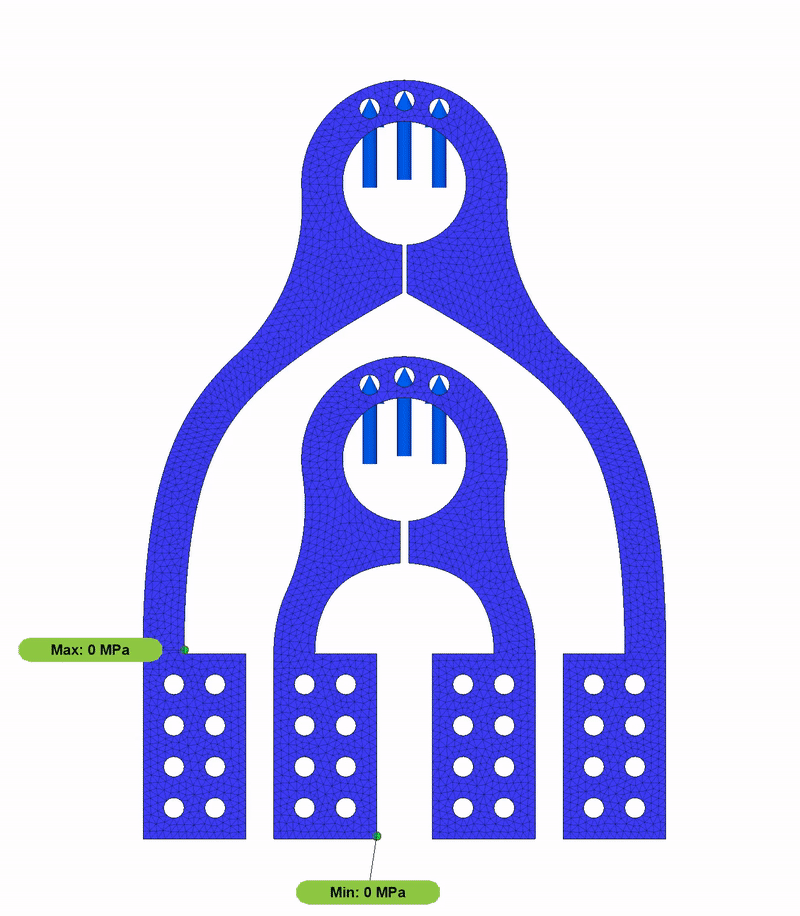

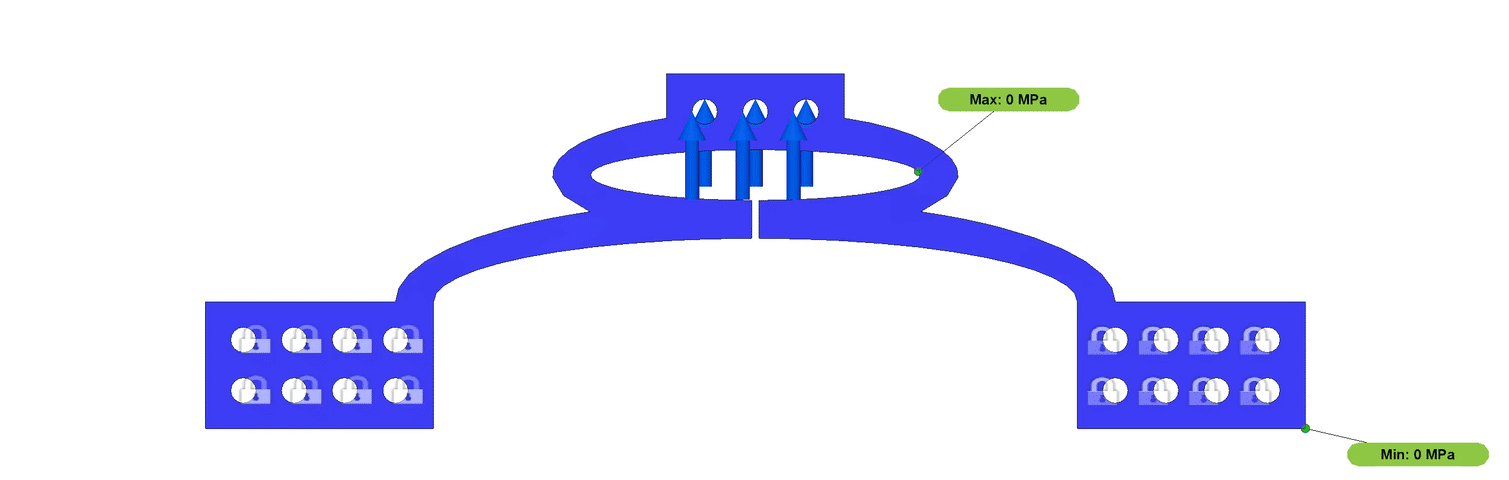
At Watchtower, we were looking for a sensor geometry that gave us better sensitivity while still being easily incorporated into silicone. We also needed a design that was only sensitive along a single axis, rejecting any signal along orthogonal axes.
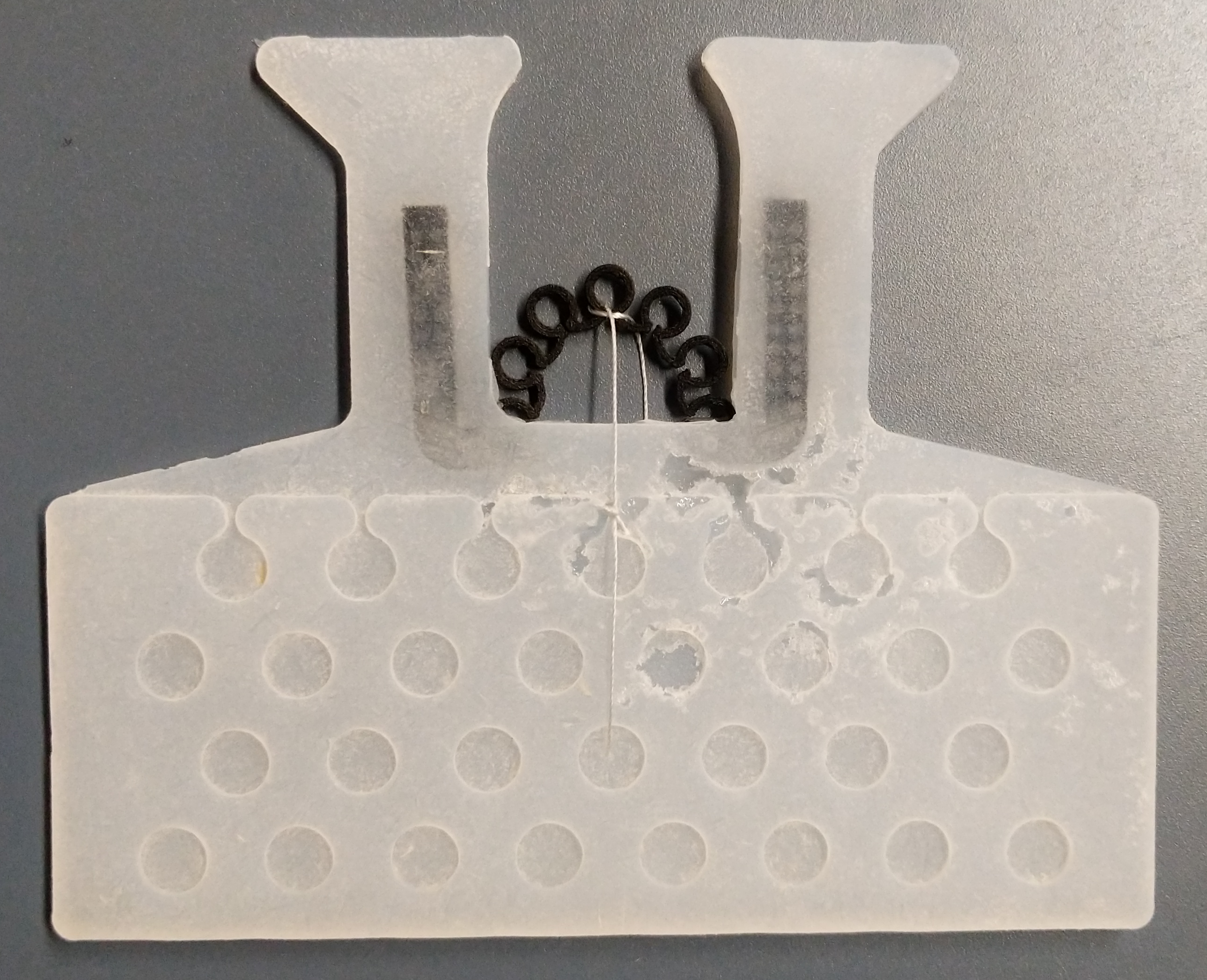
SG / 2001
An Early Prototype
The Metamaterial Strain Gauge was born out of these requirements. Made out of conductive 3D printed TPU, the strain gauge took advantage of geometries that would short together when loaded. These shorts allowed current to bypass much of the material, creating changes in resistance that were orders of magnitude larger than the changes one would get from merely stretching the material naturally. Additionally, the geometry of the sensor enabled it to only respond to forces along a defined axis. All other forces would cause the short areas to open up, preventing a change in resistance. Once the sensor was embedded into the body of the robot, it could be left in open air, placed inside a hollow cavity within the robot, or placed in a cavity filled with non-conductive mineral oil. This allows the flexural parts of the sensor to keep moving while the static parts are rigidly fixed.